How fluorite lenses are made
Canon Optron undertakes all parts of the fluorite lens production process, from crystal production to processing, grinding, and evaporation (vapor deposition).
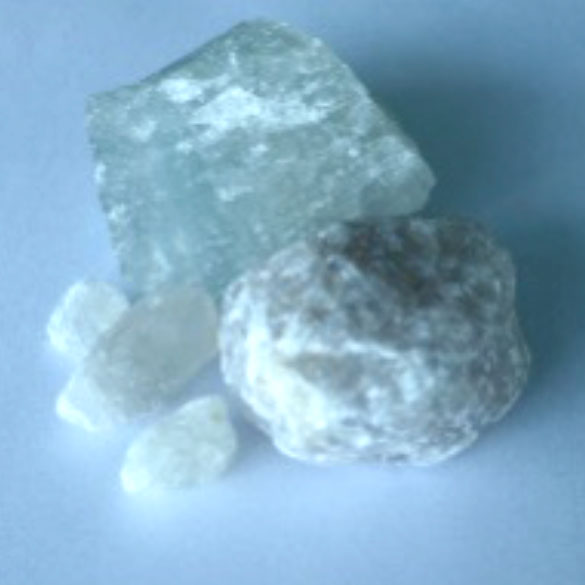
①Raw materials
Naturally occurring fluorite ore.
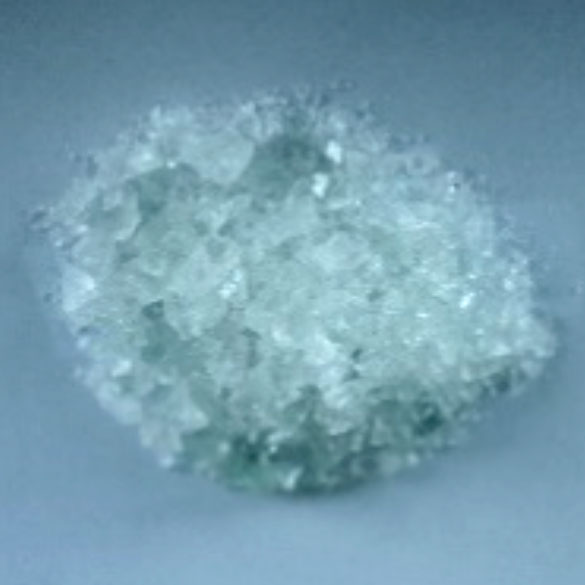
②Pulverization and refinement
The raw fluorite is pulverized into fine fragments. Impurities are then removed so that it can be used as a raw material.
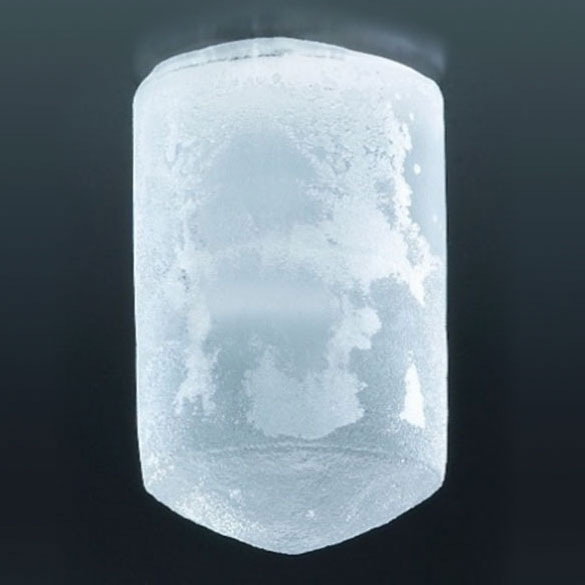
③Crystalization
The purified raw fluorite fragments are put into a crucible and melted. The crucible is moved towards the bottom of the setup so that crystallization occurs starting from the bottom. Recrystallizing the raw crystals removes impurities, creating high-purity ingots.
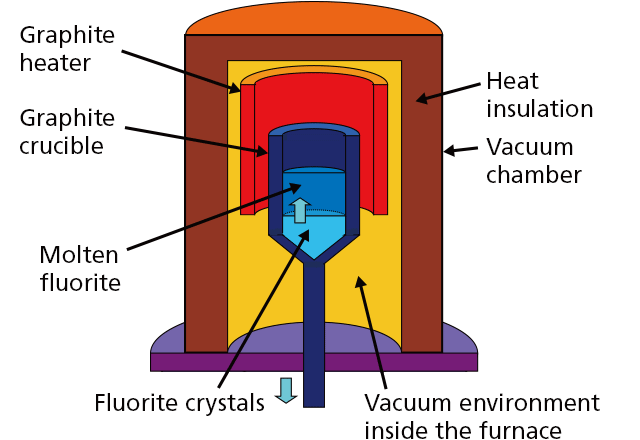
④Annealing
The crystals that are formed have distortions inside that could cause cracking if processed right away. These distortions are removed by heating the crystals to a high temperature insufficient to melt them, and then cooling them down slowly to room temperature. This process is called annealing, and takes several weeks.
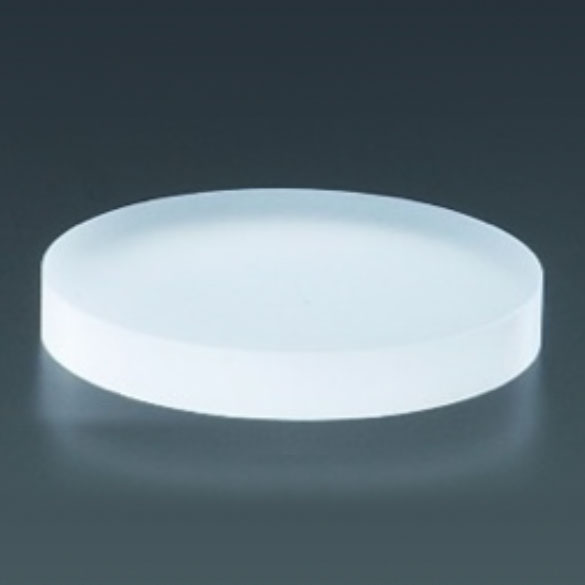
⑤Trimming and rough processing
The unnecessary parts on the surface of the crystals are trimmed off, and the crystal is rough-processed to the required size for the lens.
The interior of the crystal is inspected for anomalies.
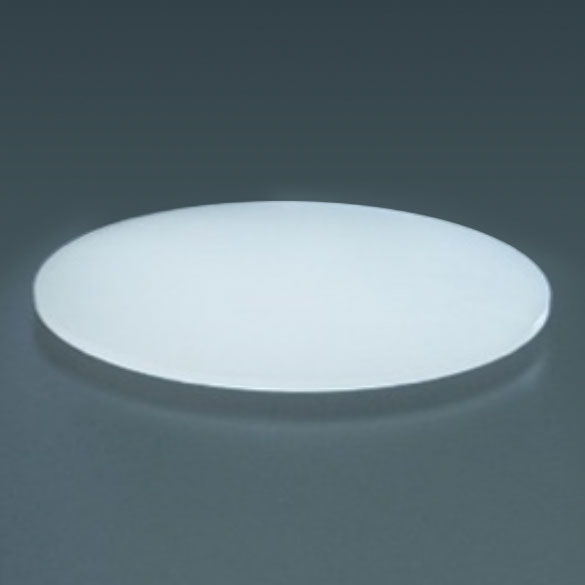
⑥Grinding
The top and bottom surfaces of the crystal are ground into a spherical shape with a surface that resembles frosted glass.
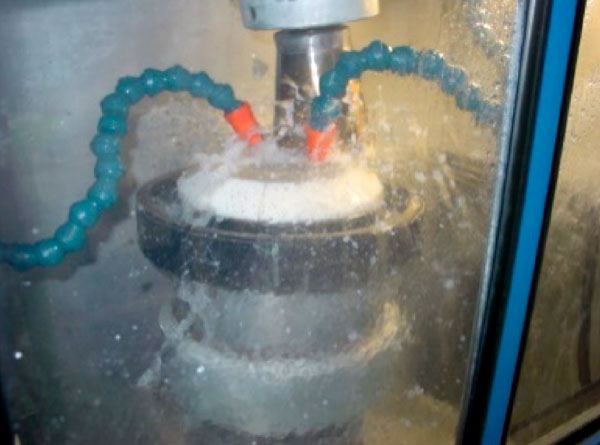
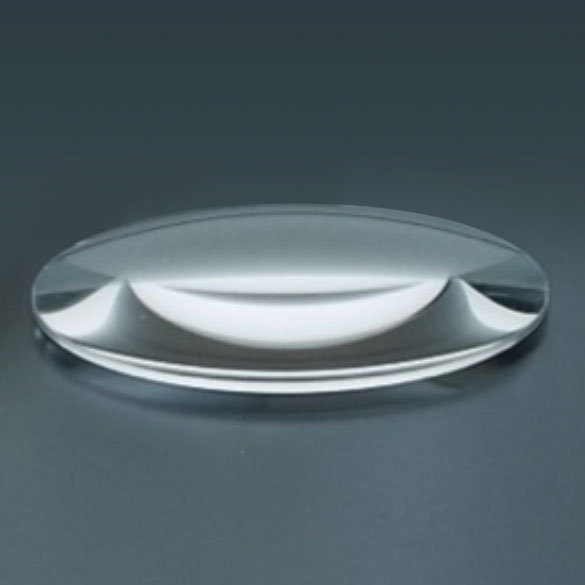
⑦Polishing
The surfaces of the crystal are polished with a pellet made from coagulated polish until they are semi-transparent and meet the specified dimensions.
Finally, a special polish is used to remove fine surface scratches.
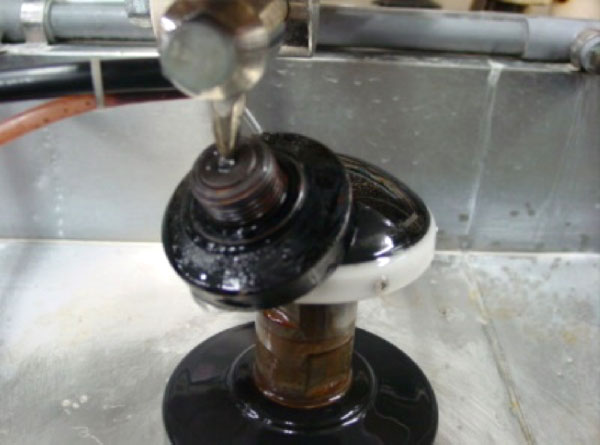
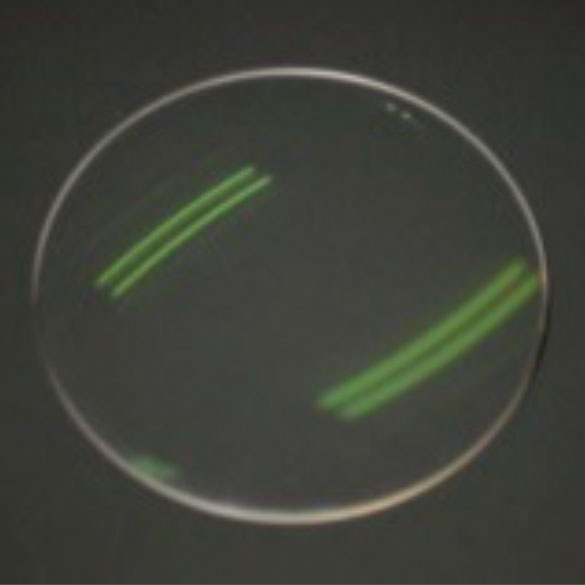
⑧Evaporation
Anti-reflective or other special coatings are applied using evaporation (also known as vapor deposition), which forms a thin film over the substrate (lens).
The raw materials used for evaporation are also produced by Canon Optron.
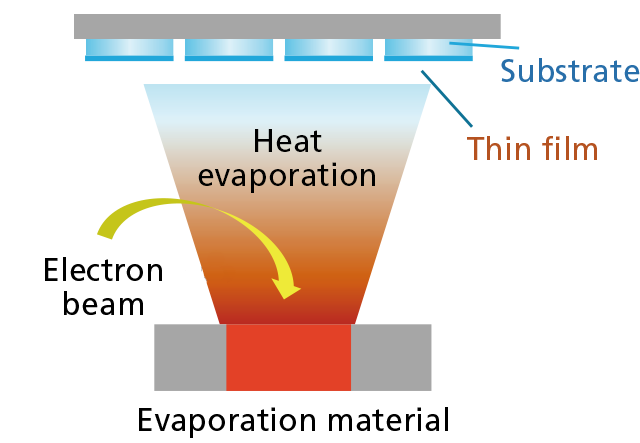
Learn more about evaporation materials here